微波裂解设备凭借独特的微波加热原理,能够将各类物料转化为有价值的产物。从生物质的深度利用到工业废料的妥善处理,它都发挥着不可替代的作用,极大地提升了资源利用率与生产效率。然而,就像再精密的仪器也会遭遇故障,微波裂解设备在运行过程中常被结焦堵塞问题所困扰,这不仅降低了设备性能,还可能导致生产停滞,带来经济损失。如何攻克这一难题,成为行业内关注的焦点。
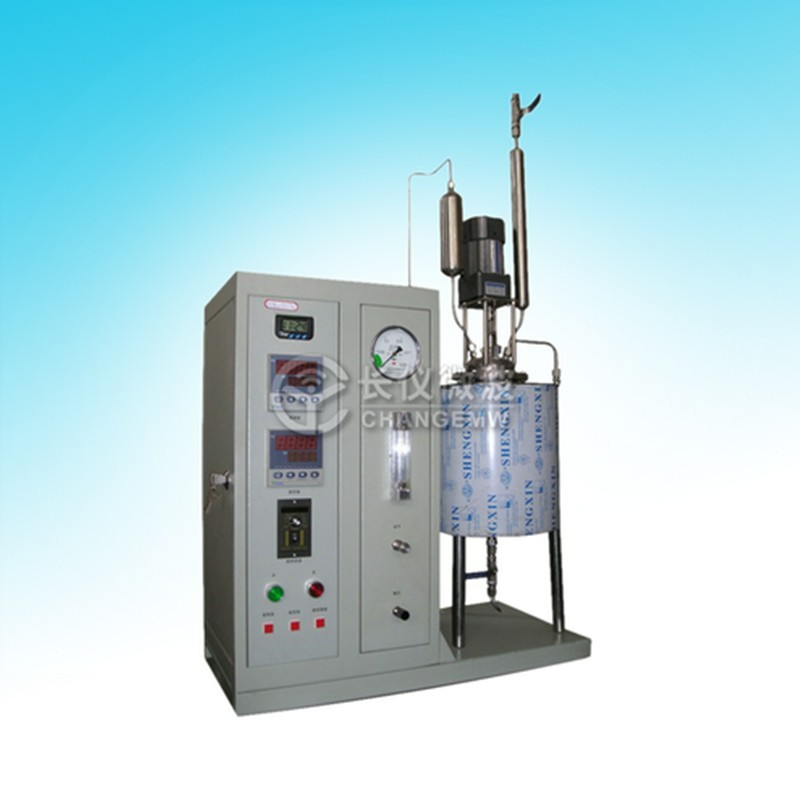
结焦堵塞原因剖析
在微波裂解过程中,物料中的有机物在高温下会发生一系列复杂反应。一方面,部分有机物可能会脱氢缩合,形成大分子的稠环芳烃类物质,随着反应的进行,这些大分子物质进一步聚合,逐渐形成焦炭。另一方面,若物料中含有一些杂质,如金属盐类等,它们可能会在微波作用下催化某些反应,促使结焦现象加剧。例如,在一些工业废盐的微波热解中,如果废盐预处理不充分,其中的杂质可能会在热解过程中引发结焦,导致设备堵塞。而且,微波加热的不均匀性也可能使得局部温度过高,加速有机物的碳化结焦,尤其是在设备的一些拐角、管道变径等位置,物料流动相对不畅,更容易发生结焦积累,久而久之就造成了设备的堵塞。
解决方案探究
优化原料预处理:对进入微波裂解设备的原料进行精细预处理是减少结焦堵塞的重要一步。对于固体物料,可通过干燥、破碎、筛分等手段,控制其湿度、粒径大小及均匀度。例如,对于生物质原料,将其水分含量控制在合适范围内,既能保证微波吸收效果,又可减少因水分过多导致的热解不完全而引发的结焦。同时,采用磁选、浮选等方法去除原料中的杂质,如金属颗粒、砂土等,避免杂质在裂解过程中催化结焦反应。通过优化原料预处理,从源头上降低结焦物质的产生,为微波裂解设备的稳定运行创造良好条件。
改进设备结构设计:合理的设备结构能有效减少物料在设备内的停留时间和流动死区,降低结焦堵塞风险。在反应器设计上,可采用特殊的结构,如带有强制推进叶片的回转窑结构,使物料在设备内均匀、快速地移动,减少局部物料堆积和过热现象。对于管道部分,尽量减少不必要的弯头和变径,采用光滑的管道内壁材质,以降低物料流动阻力,防止物料在管道内停滞结焦。此外,在易结焦的部位,如反应器底部、管道连接处等,设置可拆卸的清理装置,便于定期清理已形成的少量结焦,维持设备的正常运行。
调整工艺参数:工艺参数的精准调整对控制结焦堵塞至关重要。适当降低裂解温度,避免物料在过高温度下快速碳化结焦,但同时要确保温度满足裂解反应的基本需求。例如,在某些有机废料的微波裂解中,将温度从过高的峰值降低到适宜区间,可有效减少结焦现象,同时通过延长物料在反应器内的停留时间,保证裂解反应的充分进行。另外,合理调整微波功率,使其均匀作用于物料,避免局部功率过大导致温度过高。还可在物料中混入适量的水蒸气,水蒸气不仅能作为热载体传递热量,还能抑制碳在设备内的沉积,减少结焦的可能性。
微波裂解设备结焦堵塞问题并非无法攻克。通过优化原料预处理,从源头减少结焦隐患;改进设备结构设计,让物料在设备内流动更顺畅;精准调整工艺参数,营造适宜的反应环境,三者协同作用,为设备的稳定运行筑牢防线。