微波烧结作为一种新型的材料烧结工艺,凭借其升温速度快、能源利用率高、加热效率高以及能改善材料微观结构和性能等诸多优势,在材料制备领域得到了广泛应用。然而,随着材料科学的不断发展以及工业生产对产品质量和生产效率要求的日益提高,现有的微波烧结炉在某些方面逐渐暴露出局限性,需要进行改造升级以适应新的需求。下面将深入探讨微波烧结炉改造升级的可行方案。
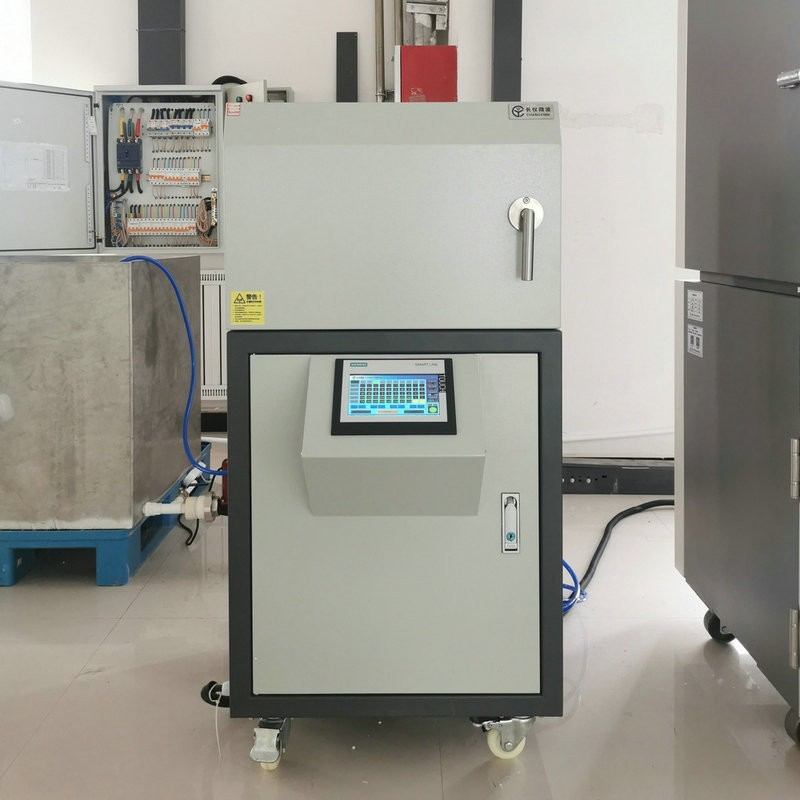
微波场优化方案
采用新型微波源
摒弃传统磁控管微波源,换装新型固态微波源。固态微波源稳定性比磁控管高出 3 - 5 倍,功率调节精度可达 ±1%,能实现 0 - 100 % 功率范围内的连续精准调控。通过精准控制输出功率与频率,可有效优化炉内微波场分布,降低微波能量反射损耗,大幅提升加热均匀性。例如,在某金属粉末烧结实验中,使用固态微波源后,物料各部位温差从原来的 ±20℃降低至 ±5℃。
优化炉体结构
重新设计炉体形状,采用如非对称六面体或带有特殊弧度的腔体结构。利用仿真软件模拟微波传播路径,合理设置内部微波反射板与吸收材料。反射板采用高反射率的金属材质,吸收材料选用新型吸波陶瓷。经实验验证,优化结构后,炉内微波场均匀性可提升 20% - 30%,复杂形状物料加热不均匀问题得到显著改善。
引入多模式微波加热
在炉体中安装多组微波激励装置,能够同时激发 TE(横电)和 TM(横磁)等多种模式微波场。通过调整不同模式微波的功率配比与相位差,让物料在多个方向均匀吸收微波能量。在陶瓷异形件烧结中应用该技术,产品合格率从 60% 提升至 85%。
能源效率提升方案
强化微波泄漏抑制
对炉门采用双层金属密封结构,中间填充吸波橡胶;观察窗使用特殊金属镀膜玻璃,既能有效屏蔽微波,又不影响观察。定期使用专 业微波泄漏检测仪进行检测,确保泄漏量远低于国家安全标准(≤5mW/cm²)。经测试,改进后微波泄漏减少80%以上,设备能源利用率提高 5%-10%。
构建余热回收系统
在冷却风道或废气排放管道上安装高效热交换器。热交换器采用翅片式结构,增大换热面积。回收的余热可用于预热物料或加热车间其他辅助设备。经测算,该措施可使微波烧结炉整体能耗降低 15% - 20%。
配备智能功率控制系统
系统基于物料温度、升温速率等参数实时调整微波源输出功率。烧结初期,以高功率快速升温;接近目标温度时,自动降低功率维持恒温。通过智能控制,能源消耗可比传统恒定功率加热方式降低 10% - 15%。
温度控制精度改进方案
换装高精度测温元件
对于表面温度测量,选用响应时间小于 0.1s、精度可达 ±0.5℃的红外测温仪;对于内部温度测量,采用高精度铠装热电偶,其测温精度可达 ±1℃,并优化安装位置,确保测量值准确反映物料实际温度。
应用先进温度控制算法
引入模糊控制算法,将温度偏差及偏差变化率模糊化处理,依据预设模糊规则实时调整微波源功率与加热时间。相比传统 PID 控制,模糊控制在复杂工况下温度控制精度从 ±3℃提升至 ±1℃以内。
建立温度场模拟模型
利用有限元分析软件,结合物料特性、微波场分布、加热过程等参数,构建炉内温度场模型。通过模拟提前优化加热工艺参数,如微波功率分布、加热时长等,并实时监测预测炉内温度变化,为温度精准控制提供有力支持。
功能拓展与集成方案
集成实时监测系统
将 X 射线衍射仪(XRD)、拉曼光谱仪等设备集成至微波烧结炉。XRD 可实时监测物料晶相转变,拉曼光谱仪能分析化学键振动情况。操作人员依据监测数据及时调整工艺参数,保障产品质量。
与其他制备技术融合
与热等静压技术集成,研发微波热等静压烧结设备,使物料在加热同时承受等静压力,提升材料致密度;与 3D 打印技术结合,实现复杂形状材料的快速烧结成型,满足个性化生产需求。
搭建远程监控与数据分析平台
借助物联网技术,实现对设备温度、功率、运行时间等参数的远程实时监测与控制。平台自动收集设备运行数据,运用数据分析算法挖掘设备运行规律与故障预警信息,助力设备维护管理与工艺持续优化。
通过对微波场优化、能源效率提升、温度控制精度改进以及功能拓展与集成等多个方面的改造升级方案探讨,可以有效解决现有微波烧结炉存在的加热不均匀、能源效率低、温度控制精度不足以及功能单一等问题。这些改造升级方案不仅能够提高微波烧结炉的性能和生产效率,降低生产成本,还能满足材料科学不断发展对设备提出的更高要求,推动微波烧结技术在更多领域的广泛应用和进一步发展。在实际实施改造升级项目时,应根据具体的生产需求、设备现状以及经济成本等因素综合考虑,选择合适的改造方案组合,以实现最佳的改造效果。